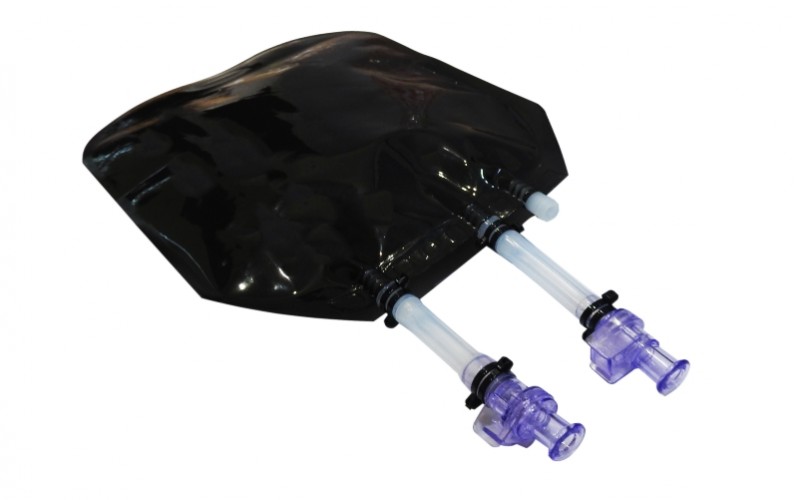
Many biopharmaceutical drug substance/products, process intermediates and chemically defined media (for mammalian cell culture) are light sensitive.
Exposure of light sensitive drugs to UV or visible light, may result in degradation of drug molecules that may impact patient safety. In case of light sensitive media, degradation of vital ingredients such as vitamins can reduce process efficiencies in mammalian cell expression systems.*
AseptiBag™ ULO+ are designed to protect light sensitive fluids with a unique layer for minimizing UV and light transmission.
Continue reading “AseptiBag™ ULO+ 2D Single Use Systems for Storage and Transfer of Light Sensitive Fluids”